Spotlight
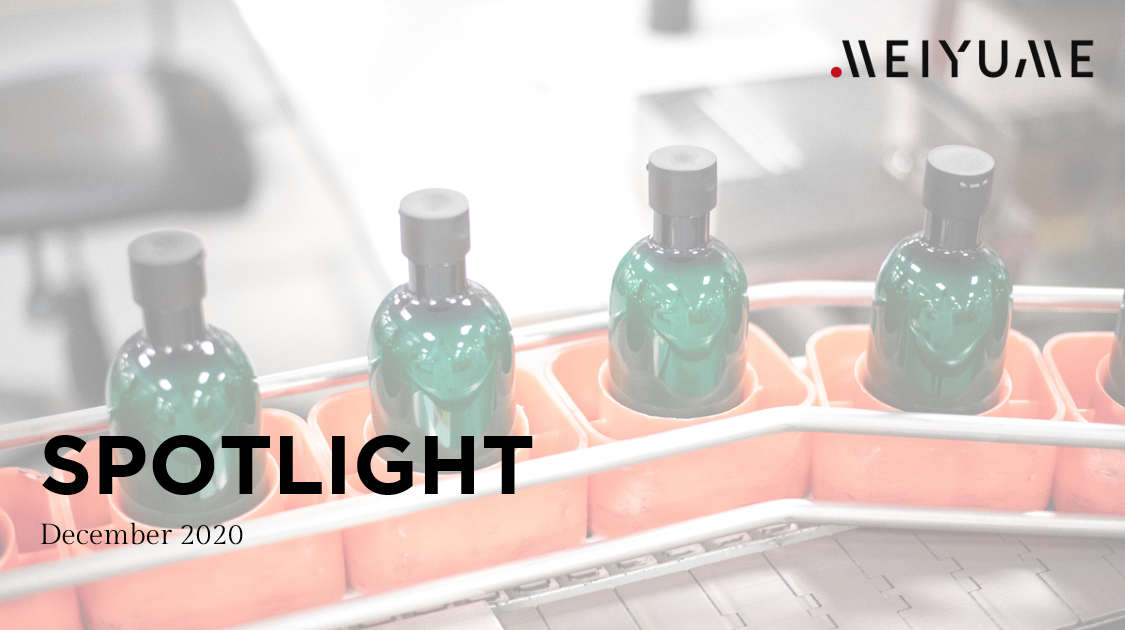
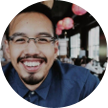
Joachim Gregory, Project Manager in Meiyume’s Global Manufacturing Operations, talks to us about some of the challenges we have faced during the pandemic and how Meiyume is transforming operations for the future.
1. Tell us more about your role!
I am currently a Project Manager in Meiyume’s Global Manufacturing Operations. My role consists of managing projects which are essentially any major endeavors to achieve a certain outcome within a time frame and/or budget. In other words, I help our company spend money efficiently to achieve a goal within the shortest period of time.
As a Project Manager, I oversee the entirety of a project from its beginning up to when its targeted deliverables are achieved. In the case of our Global Manufacturing Operations, projects may consist of Improvement Initiatives, Cost Saving Initiatives, Capacity Upgrades, and more. Some specific examples include improving an OEE (Overall Equipment Effectiveness) of a machine or system, decreasing the power consumption of our factories by implementing energy saving initiatives, implementing a new manufacturing line, or even building a whole new factory from the ground up!
Each project has varying scopes – design, construction, regulatory, safety, supply chain set-up, installations, testing & commissioning, validations – and this is where I come in to ensure that each aspect achieves their respective targets and align harmoniously within a deadline.
2. What are some capabilities that are specific to our Indonesia plant?
Our Indonesia manufacturing operations located in Jakarta is very similar to our other manufacturing sites in terms of its service offerings – ranging from Product Development to Manufacturing, Quality Assurances, Warehousing and Transportation.
Nonetheless, we do have some added capabilities that makes our Indonesia operations special, such as being the only fully Halal Certified Site in Meiyume, giving it great prospects in the ever-growing Halal market.
It also has one of the most diverse range of manufacturing capabilities which consist of Skin Care, Hair Care, Personal Care, Color Cosmetics, Oral Care and Fragrances. Not all sites have such a diverse range of manufacturing capabilities and we are further expanding it with a Mouthwash manufacturing line that will be in production next year!
Furthermore, it has the capability to cater to small MOQs for indie brands and smaller private labels. This demand has been steadily growing and currently makes up for approximately 20% of the Indonesia plant’s portfolio.
3. Can you tell us more about how the pandemic has shifted our production?
Like most businesses, our manufacturing sector was impacted by the pandemic. There was a major drop in demand for certain products especially in the beauty sector. With the movement control orders that came into force, people are encouraged to stay home and consequently, this has led to a decrease in the usage of cosmetics and fragrances.
Nonetheless, there are silver linings. Since there is an increased awareness on the importance of hygiene and sanitization, there has been a surge in demand for sanitizers and personal care products.
Since the pandemic, our team started re-evaluating ways to further improve existing capabilities and facilities so that we emerge stronger from this. For example, our Trowbridge manufacturing site recently completed a 3-month initiative that resulted in more than 30% improvement in our mixing batch cycle time for major product formulas.
4. What measures have we taken to ensure that our colleagues in the factories are working in a safe environment in these unusual times?
I believe all of our factories have high health and safety standards to ensure a safe working environment for us.
We have strict procedures and guidelines aligned to local regulations. For example, all individuals are required to do a body temperature check upon entry into our premise. There is also a “low COVID risk” declaration form to be signed daily. As an added initiative, we have set up a sanitization mist booth at the factory entrances to ensure every person who enters the premise are fully sanitized from head to toe.
We also implemented social distancing by minimizing the number of employees on site through rotational work-from-home schedules, and we have expanded our common areas such as the canteen to ensure that social distancing is always practiced even during break times.
Another practice employed is the sanitization of our production lines at every shift to ensure that any potential contamination from one shift does not spread to the next.
5. What are some exciting developments you are seeing across our factories and what are some trends you think will be here to stay?
In the history of manufacturing, we have passed 3 stages of industrialization and have entered the 4th Industrial Revolution, or better known as “Industry 4.0”. This industry revolution basically focuses on integrating cyber physical systems, IIOT (Industrial Internet of Things), Cloud Computing and Cognitive Computing into our industries and Meiyume is joining this revolution.
We are currently working on having our sites upgraded so that our manufacturing lines are self-recording, tabulating and reporting. More importantly, all of this information will be available at the tip of our fingers via the internet anywhere and anytime. This is an exciting and game-changing initiative that will be implemented across all our factories in the coming years.